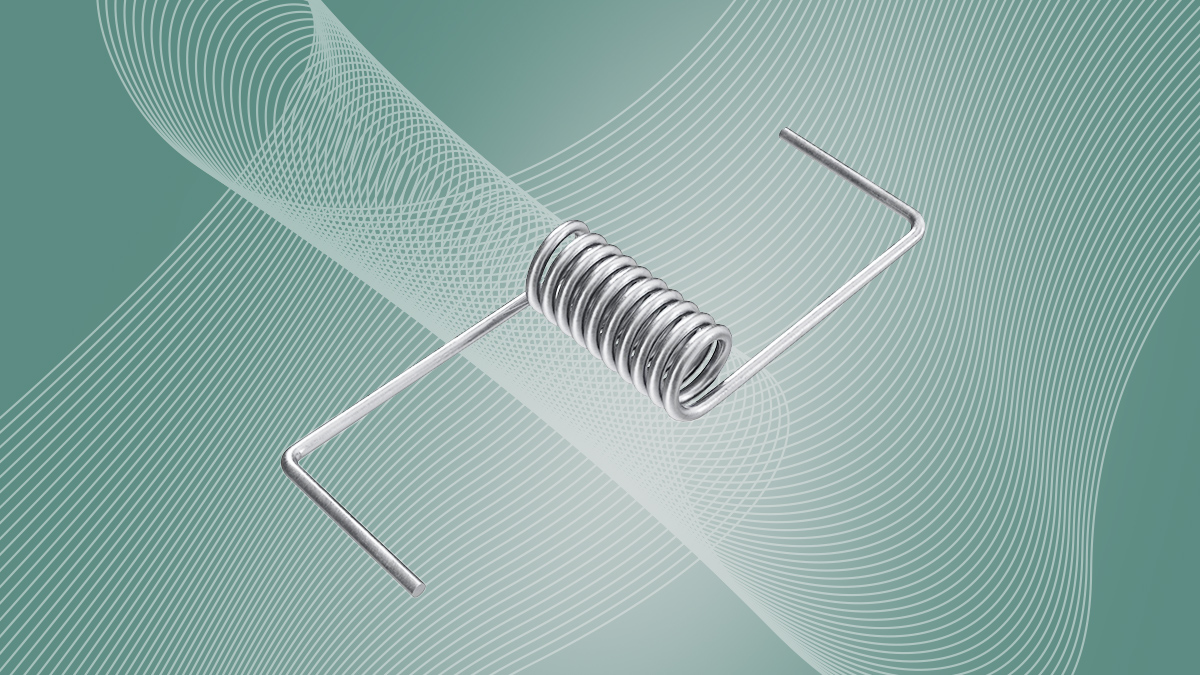
Imagine a high-volume automotive assembly line suddenly grinding to a halt because a critical conveyor system’s torsion spring has failed. Each minute of downtime costs thousands in lost production, and the maintenance team scrambles to replace the component. Or consider a precision electronics manufacturer discovering that a batch of testing equipment is producing inconsistent results because poorly manufactured springs in their calibration mechanisms have weakened over time, potentially compromising quality control for thousands of units.
These scenarios play out more often than many manufacturers care to admit, highlighting why the quality of even seemingly simple components like torsion springs can have outsized impacts on operational efficiency and product reliability. Manufacturing high-quality torsion springs requires precise engineering, careful material selection and strict adherence to design principles. These mechanical components play a crucial role across various industries, from automotive applications to consumer electronics. Understanding the key factors in their production helps ensure reliability and longevity in their performance.
What is a torsion spring
A torsion spring is an engineered, designed mechanical component that stores and releases energy through rotational motion. Unlike compression or extension springs that work along a linear axis, these helical devices operate by twisting around their axis. When force is applied, the coils of the spring wind tighter, creating stored energy that can be released when needed. The unique design allows these mechanical components to deliver consistent torque while maintaining structural integrity throughout their operational lifetime.
What is the function of torsional springs
These versatile mechanical components serve multiple purposes across diverse applications. In garage doors, the coiled mechanism counterbalances the door’s weight, making it easier to open and close. Automotive manufacturers rely on these rotational springs in their suspension systems, helping to absorb road shock and maintain vehicle stability. In consumer electronics, smaller variants provide the necessary resistance in flip phones, laptop hinges and gaming controllers.
The primary function revolves around torque generation and energy storage. When properly engineered, these mechanical coils can:
- Generate consistent rotational force
- Maintain precise positioning
- Provide controlled resistance
- Support weight counterbalancing
- Enable smooth mechanical transitions
What is the life expectancy of a torsion spring
The operational lifespan of a torsion spring depends heavily on several factors, including usage patterns, environmental conditions and manufacturing quality. Under optimal conditions and proper installation, these mechanical components typically last between 15,000 and 20,000 cycles. However, some specialized designs can achieve upwards of 100,000 cycles when manufactured with premium materials and advanced engineering techniques.
Critical manufacturing factors for durability
Material selection
The choice of material significantly impacts spring performance and longevity. High-grade spring steel remains the industry standard, with optional alloys available when a project demands more stringent performance characteristics. Each material brings unique properties to a project. For example, stainless steel offers corrosion resistance, perfect for marine or outdoor environments.
Winding direction and technique
The winding process requires precise control and expertise. The direction of winding affects how the spring responds to applied forces and proper technique ensures uniform coil spacing and tension distribution. Advanced manufacturing facilities employ computer-controlled winding machines to maintain consistency and precision throughout production.
Heat treatment and stress relief
Proper heat treatment is essential for achieving optimal mechanical properties. The process involves carefully controlled heating and cooling cycles that enhance the spring’s strength and durability. Stress relief procedures prevent premature failure by removing internal stresses created during the manufacturing process.
Surface treatment and finishing
Surface finishing protects against corrosion and reduces friction between coils. Common treatments include:
- Shot peening to improve fatigue resistance
- Zinc or nickel plating for corrosion protection
- Powder coating for aesthetic and protective purposes
Load capacity optimization
Engineers must carefully calculate and test the spring’s load-bearing capabilities. Proper design ensures the component operates within its elastic limit, preventing permanent deformation. Factors considered include:
- Maximum stress levels under peak loads
- Operating temperature range
- Required deflection angles
- Safety margins for unexpected loads
Quality control measures
Implementing stringent quality control throughout the manufacturing process ensures consistency and reliability. This includes:
- Material certification and testing
- Dimensional verification
- Load testing at multiple angles
- Fatigue testing for life cycle estimation
By carefully considering and controlling these factors during manufacturing, producers can create torsion springs that deliver reliable performance throughout their intended service life. The investment in quality materials, precise manufacturing processes and thorough testing procedures results in components that meet or exceed industry standards for durability and reliability.
Partner with experience
When precision and reliability matter to your bottom line, partnering with an experienced spring manufacturer makes the difference between consistent performance and costly failures. Elyria Spring & Stamping brings decades of expertise to every project, offering custom spring solutions that often prove more cost-effective than stock alternatives.
Our in-house prototyping capabilities and skilled craftsmen can transform your specifications into precisely engineered components, whether you need a short production run or long-term manufacturing partner. Don’t let spring performance put your operations at risk – contact Elyria Spring & Stamping today to discuss your custom spring requirements and discover why industry leaders trust our team for their most demanding applications.