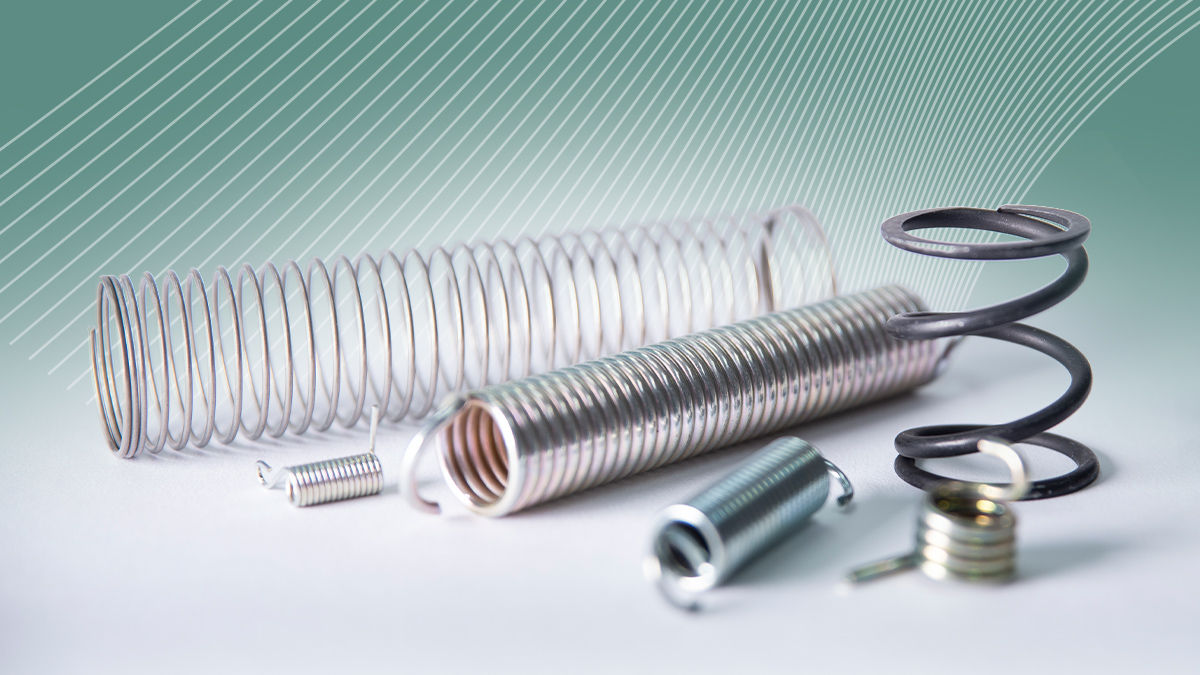
When designing a mechanical system, engineers should understand the operating length of the springs designated for insertion into that system. This fundamental parameter, along with other critical dimensions, determines the spring’s functionality, durability and reliability across various applications.
Miscalculating a spring’s operating length can lead to significant issues in mechanical systems. For example, if the spring is too short, it may become overcompressed, leading to permanent deformation and potential failure. Conversely, if the spring is too long, it could interfere with surrounding components, causing assembly problems or inhibiting proper function. Spring failure can even cause the entire system to fail prematurely. This unplanned downtime can be extremely costly in terms of lost production, maintenance expenses and potential safety risks.
These problems are especially critical in industries like automotive, aerospace and industrial machinery, where spring components must operate reliably under demanding conditions. Incorrect spring length can result in decreased performance, shortened service life and even safety hazards. Within overall design, springs can be overlooked, but even a component small in size can misrepresent the critical role it plays in operational performance. Careful analysis of factors like load, deflection and environmental conditions is essential to ensure reliable, long-lasting performance.
What is the operating length for a spring?
The operating length of a spring refers to its installed length when subjected to normal working conditions. This dimension directly impacts the spring’s performance characteristics and its ability to maintain specified force requirements throughout its service life. Determining the appropriate operating length requires considering factors such as material properties, wire diameter, coil geometry, operating environment, cyclic loading, force output, and installation constraints.
What is the load length of a spring?
The load length is the length of the spring when it is compressed or extended under a specific applied force. This parameter differs from the free length (unloaded length) and is essential for several reasons:
- Performance Verification: Load length data allows engineers to confirm if the spring meets design specifications under working loads.
- Stress Analysis: Knowing the load length enables the calculation of material stress levels during operation.
- Fatigue Life Prediction: Load length information assists in estimating the spring’s service life.
- Assembly Requirements: The load length ensures the spring will fit properly within the mechanical assembly.
Thinking about the link between load length and operating length can help avoid complications. These problems include over-compression, permanent deformation, early failure and interference with nearby parts.
How do you calculate spring length?
Spring length calculations include several important factors. These factors are free length, solid length, number of active coils, wire diameter and mean coil diameter. The basic formula for calculating spring length under load is:
L = Lf – (F × k)
- L = Length under load
- F = Applied force
- k = Spring rate (force per unit deflection)
Beyond these basic calculations, professional spring design for industrial applications requires addressing several advanced factors:
- Material Selection: The spring material must have the appropriate fatigue resistance, environmental compatibility, temperature characteristics and corrosion resistance for the application.
- Manufacturing Tolerances: Tight control over dimensional accuracy, surface finish and heat treatment specifications is essential for consistent spring performance.
- Quality Control Requirements: Manufacturers like Elyria Spring & Stamping maintain comprehensive quality systems to meet PPAP Level 3 standards. This includes cross-functional teams, detailed documentation and compliance with AIAG requirements. Automotive and other industrial customers often require this compliance.
- Tool and Die Considerations: Modern spring manufacturing leverages advanced capabilities, such as 3D modeling, automated production, tool modification and precision die fabrication. Elyria Spring’s in-house tool and die shop allows them to keep costs low and respond quickly to customer needs.
Practical selection guidelines
When choosing the appropriate spring operating length, engineers should follow these steps:
- Define Operating Parameters
- Maximum and minimum working loads determine the required force capacity of the spring.
- The required deflection range ensures the spring can accommodate the necessary motion without exceeding stress limits.
- Operating temperature range helps select materials that can withstand the environmental conditions.
- Environmental conditions like exposure to chemicals, moisture or vibration may necessitate special materials or coatings.
- Consider Installation Requirements
- Available space envelope dictates the maximum physical dimensions the spring can occupy.
- Mounting configuration affects how the spring interfaces with other components.
- Assembly/maintenance access impacts the spring’s accessibility for installation and servicing.
- Interface with mating components requires clearance and compatibility planning.
- Evaluate Performance Criteria
- Required service life determines the spring’s fatigue resistance and durability needs.
- Load stability requirements ensure consistent force output over the spring’s lifespan.
- Tolerance stack-up effects account for manufacturing variations in the overall system.
- Dynamic response characteristics address any vibration, shock or cyclic loading concerns.
- Verify Manufacturing Capabilities
- Optimal tooling design enables the production of springs to tight tolerances.
- Efficient production processes help control costs and lead times.
- Comprehensive quality control ensures consistent performance and reliability.
- Reliable documentation supports application-specific design validation.
Elyria Spring & Stamping’s expertise in these areas can provide valuable support. Their cross-functional team approach and adherence to PPAP Level 3 requirements ensure springs meet both technical specifications and quality standards. Additionally, their in-house tool and die capabilities allow for efficient prototyping, modification and production of custom spring designs.
Making the right decision specifying spring length
Selecting the appropriate spring operating length is a crucial step in designing reliable mechanical systems. Engineers can ensure springs perform well by understanding what affects their length. They use advanced calculation methods and collaborate with skilled manufacturers. This approach helps maintain quality and durability. The combination of technical analysis, quality manufacturing and comprehensive testing protocols results in spring components that provide long-lasting, dependable service in demanding industrial applications.
For more than 75 years, Elyria Spring & Stamping has been a trusted partner for hundreds of companies seeking reliable components and dedicated customer service. Contact us today to discuss your application.