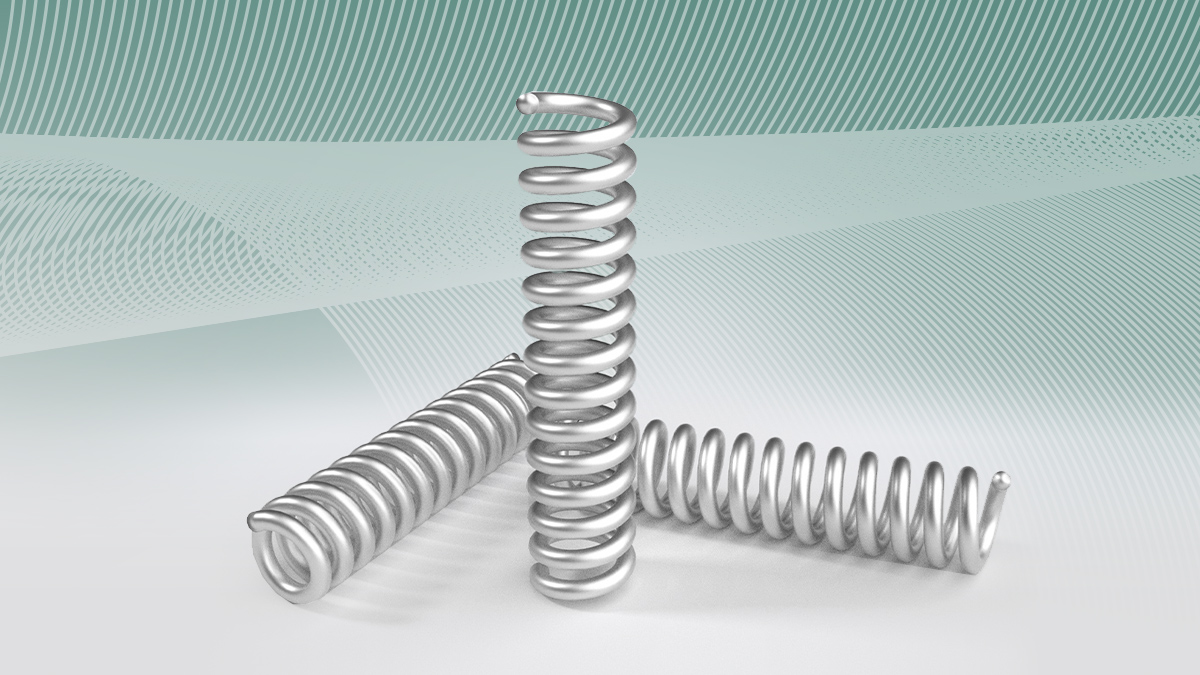
Medical manufacturers rely on compression springs for precise, repeatable pressure control in surgical instruments or laparoscopic devices. Ever clicked a pen while concentrating on a task? A compression spring extends and retracts the pen tip. Or recall a classic example of a compression spring at work from your childhood if you ever bounced on a pogo stick. Even typing this article, compression springs are in action in my keyboard, to provide tactile feedback and resistance when pressing the keys.
When it comes to spring design, compression springs present a uniquely versatile option that offer unique features and benefits compared to other spring types like torsion and extension springs. The compression properties of springs make them suitable for a wide range of applications, particularly in industries requiring precise force and energy management. Recent market research suggests compression springs overall are anticipated to exhibit a 5.0% CAGR through 2031, driven by demand from the transportation, manufacturing and petrochemical sectors.
Understanding the compression rate of springs
At the core of what makes compression springs unique is their compression rate – the amount of force required to compress the spring a given distance. As the spring is compressed or pressed down, the spring stores the potential energy created in compression and then releases that energy when the force compressing the spring is removed.
The compression rate of a spring is calculated as the spring rate, or the amount of force required to compress the spring one unit of distance. There are different mathematical equations to express the measure of a spring’s stiffness and the force required to compress a spring. Newtons indicate the force required to stretch or compress a spring by one millimeter. For instance, a spring with a rate of 10 N/mm will require 10 Newtons of force to stretch or compress the spring by one millimeter.
This compression rate can be precisely engineered by adjusting the spring’s material, diameter, coil count and other key parameters. These factors help with compression spring selection for an application because the spring must be able to support the anticipated loads without exceeding its design limits.
In contrast, torsion springs primarily resist twisting forces, while extension springs are designed to resist pulling or tensile forces. The compression properties of springs make them ideally suited for applications where consistent, controlled force is critical.
What happens if you compress a spring too much
While compression springs are designed to withstand significant compressive loads, compressing them beyond their rated capacity can lead to permanent deformation or even breakage. When a compression spring is compressed too far, the coils begin to touch each other, dramatically increasing the spring rate and the stress on the material. This can cause the spring to take on a “solid height”, a term used to describe the point at which the coils are fully compressed with no more room for further compression, indicating potential damage to the spring.
Exceeding the solid height of a compression spring often results in permanent set, where the spring does not fully return to its original length even after the compressive force is removed. In extreme cases, excessive compression can lead to the spring buckling or breaking entirely.
When specifying a compression spring for a project, these issues can be avoided by carefully selecting a spring rated for the specific loads and requirements of the application. Best practice is to work with a company that specializes in spring manufacturing such as Elyria Spring to help guide spring selection that meets requirements for expected compression.
Are springs better in tension or compression
Among the many spring types, both compression and tension (extension) springs play different yet important roles. Again, the choice depends on the specific application requirements. In general, compression springs are better suited for applications where the spring experiences compressive forces, such as in suspension systems, machinery and tools. The compression properties of these springs allow them to provide consistent, controlled resistance to pressing or pushing forces.
Tension springs, on the other hand, are better suited for applications where the spring experiences pulling or stretching forces, such as in latches, clutches and supports. Torsion springs, which resist twisting motions, find use in hinges, valves and other mechanisms that require a twisting action.
The decision between compression, tension or torsion springs comes down to the specific force requirements of the application. For instance, in a suspension system, the spring must be able to support the weight of the vehicle without bottoming out, making compression springs an ideal choice. Compression springs excel when consistent, reliable resistance to compressive loads is needed, making them a popular choice across many industries.
Compression springs in industrial applications
The unique compression properties of springs make them ideal for a wide range of industrial applications that require precise force management. In manufacturing equipment, this type of spring plays an important role in shock absorbers, dampers and suspension systems to provide controlled resistance to impacts and vibrations. This helps protect sensitive components and ensures smooth, reliable operation.
Compression springs are also widely used in tools and machinery where consistent clamping, gripping or pushing forces are essential. Equipment like clamps, jigs, valves and actuators rely on the compression springs for repeatable performance. Additionally, these components play a critical role in precision measuring and testing equipment, for their ability to provide a known, predictable force.
Beyond industrial applications, compression springs are found in everyday consumer products as well. Automotive suspensions, office chairs, kitchen appliances and even musical instruments all utilize the compression properties of springs to enhance functionality, performance and best use practices.
Custom spring capabilities
Elyria Spring has been specializing in custom compression spring manufacturing since 1947, offering its customers a full-service solution that goes beyond just producing parts. As an expert compression spring manufacturer, Elyria Spring can create prototypes using their rapid prototyping process, produce specialized spring varieties and provide the product in a wide range of materials and finishes.
Elyria Spring manufactures compression springs in a variety of specialized types, including:
- Cylindrical
- Conical or barrel (convex) shaped springs
- Concave (hourglass)
- Variable rate
- Miniature
This breadth of custom manufacturing capabilities allows Elyria Spring to solve even the most difficult design challenges, delivering the optimal solution for each customer’s unique application requirements.
Selecting the right compression spring
When choosing a compression spring for an application, there are several key factors to consider beyond just the compression rate. The spring material, finish, size and shape all play a role in determining its suitability. Stainless steel or alloys offer varying degrees of strength, corrosion resistance and fatigue life. The spring’s shape, such as cylindrical or conical for example, affects compression characteristics and space requirements.
Working with an experienced manufacturer like Elyria Spring helps companies select the right spring for the application. Expert assistance can help evaluate the application requirements, recommend the optimal spring design and provide guidance on proper installation and usage. By collaborating closely with the spring supplier, design engineers and purchasing agents can source the right solution that will provide a memorable experience by sourcing a component that is easy to forget, due to its extended lifespan of trouble-free service.
For more than 75 years, Elyria Spring & Stamping has been a trusted partner for hundreds of companies seeking reliable components and dedicated customer service. Contact us today to discuss your application.